|
|
|
Polyester
(PET)

Polyester
yarn and fiber
Introduction
Polyester began as a group of polymers in W.H.
Carothers' laboratory. Carothers was working for DuPont at the time when
he discovered that alcohols and carboxyl acids could be successfully
combined to form fibers. Polyester was put on the back burner, however,
once Carothers discovered nylon. A group of British scientists--J.R.
Whinfield, J.T. Dickson, W.K. Birtwhistle, and C.G. Ritchie--took up
Carothers' work in 1939. In 1941 they created the first polyester fiber
called Terylene. In 1946 DuPont bought all legal rights from the Brits and
came up with another polyester fiber which they named Dacron.
In 1958 another polyester fiber called Kodel was
developed by Eastman Chemical Products, Inc. The polyester market kept
expanding. Since it was such an inexpensive and durable fiber, many small
textile mills emerged all over the country--many located in old gas
stations--to produce cheap polyester apparel items. Polyester experienced
a constant growth until the 1970s when sales drastically declined due to
the negative public image that emerged in the late 60s as a result of the
infamous polyester double-knit fabric!
Today, polyester is still widely regarded as a
"cheap, uncomfortable" fiber, but even now this image is slowly
beginning to change with the emergence of polyester luxury fibers such as
polyester micro fiber.
Polyester is currently defined as: "Long-chain
polymers chemically composed of at least 85 percent by weight of an ester
and a di-hydric alcohol and a terephthalic acid." The name
"polyester" refers to the linkage of several monomers (esters)
within the fiber. Esters are formed when alcohol reacts with a carboxylic
acid.
There are many possible variations of the generic
polyester fiber. Two that are currently produced commercially are
polyethylene terephthalate (PET) and poly-1,4, cyclohexylene dimethylene
(PCDT). A third polyester fiber, polyethylene oxybenzoate (PEB) was
manufactured in Japan during the 1970s and early 1980s under the trade
name A-Tell®. Production of this fiber was discontinued, because it did
not offer enough performance advantages to remain competitive in the
textile market.
|
Properties
Specific weight |
1,22 to 1,38 g/cm3 |
Tenacity |
up to 85 cN/tex |
Moisture regain |
0,2 - 0,5 % |
Effects to heat |
ironing temperature 150 - 200° C
melts at 249 - 288° C |
- strong
- resistant to stretching and shrinking
- resistant to most chemicals
- quick drying
- crisp and resilient when wet or dry
- wrinkle resistant
- mildew resistant
- abrasion resistant
- able to retain heat-set pleats and
creases
- easily washed
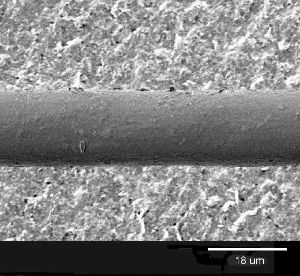
|
Applications
Because of their many desirable qualities, polyester
fibers and fabrics have many uses.
Polyester is often used in outerwear because of its
high tenacity and durability. It is a strong fiber and consequently can
withstand strong and repetitive movements. Its hydrophobic property makes
it ideal for garments and jackets that are to be used in wet or damp
environments - coating the fabric with a water-resistant finish
intensifies this effect.
Many jackets and quilted garments are made of
polyester. Since polyester can be molded into almost any shape, certain
insulating properties can be built-in to the fiber. One method is to
create hollow fibers:
This process traps air inside the fiber which is
then heated by the body. The warm air stays inside and helps warm the body
in cool weather. A second method is to use crimped polyester in a
fiberfill product. The crimp helps to keep in warm air. Polyester is an
ideal fiber to use for this since it will retain its shape, unlike its
cotton and wool counterparts that tend to flatten out over time,
significantly reducing their ability to trap warm air.
Polyester is used in pants, shirts, suits, and bed
sheets either by itself or as a blend, because of its wrinkle-resistant
property and its ability to retain its shape. Since these garments are
frequently worn and washed, its stain-resistance and durability are also
desirable.
Polyester also has industrial uses as well, such as
carpets, filters, synthetic artery replacements, ropes, and films.
|
For every form of clothing |
|
carpets, curtains,
draperies, sheets and pillow cases, wall coverings and upholstery |
|
fiberfill for various
products; automobile upholstery, fire hose, power belting, ropes and
nets, sewing thread, tire cord, sails, v-belts, floppy disk liners |
|
Grades
|
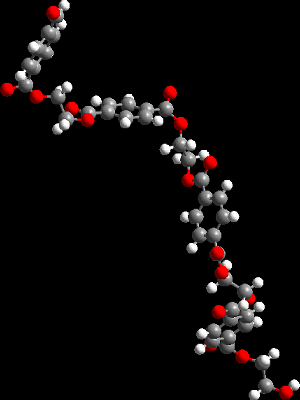 |
Processability
Most polyesters are made from petroleum from which
the constituent acids and alcohols are derived. The types of processes
that manufacturers use vary, and little is known about specific
manufacturing processes, because the companies want to keep them a secret
in order to remain competitive. Here is a general description of how
polyester is synthesized:
1) Polymerization
Condensation polymerization occurs when the acid and alcohol are reacted
in a vacuum at high temperatures. The polymerized material is extruded in
the form of a ribbon onto a casting trough or cooling wheel. After the
ribbon hardens, it is cut into chips.
2) Spinning
The chips are dried and then put into hopper reservoirs for melting.
Polyester is a "melt spun" fiber, which means that it is heated,
extruded through the spinnerets, and cools upon hitting the air. From
there it is wound around cylinders.
3) Drawing
The fibers are then hot stretched until they are about five times their
original length in order to decrease their width. The drawing results in a
optimal orientation of the molecules inside the fiber and results in a
perfect strength.
Variations on the Basic Polyester
Different fibers can be created by doing one or more
of the following:
- Adding a delusterant (dulling agent) -
Polyester is a naturally bright fiber, but can be made dull or
semi-dull by the addition of a TiO2.
- Changing the shape of the holes in the spinneret
The simplest and most common shape is a circle, but by changing the
shape of the spinneret, square, oval, and bean-shaped fibers can be
formed. One can even create a hollow fiber. The different shapes
affect the hand and strength of the fiber.
- Drawing it out more
Drawing out the fiber to five times its original length is normal, but
polyester can be stretched even further. Drawing it out more than
normal may also affect the strength, elasticity, and dye-ability.
- Adding dye stuffs
In its natural state, polyester is a slightly transparent off-white.
Adding dye stuffs at the manufacturing stage can create brilliant
colors like electric blue and atomic red. In this field Setila
is one of the World leader with its DECORA
programme, especially for the automotive industry where extremely high
fastness requirements are demanded
- Crimping
When the fiber is drawn out it is long and smooth. Crimping can give
the fiber more texture and bulk and can increase its insulation
properties, as well as its elasticity. Another word for this is
texturizing.
Making Yarns
After the fiber itself is created, it is made into a
yarn. There are two types of polyester yarns: filament and spun.
Filament yarns are made by taking the single
polyester filaments, grouping them together and then twisting or
air-entangling them to make them workable. A monofilament yarn has just
one, single polyester fiber that is usually not twisted.
Spun yarns are produced in much the same way as a
cotton or wool yarn is produced. The long filaments are fist cut into
short pieces called staple. These are then combined together and spun to
create a yarn made up of thousands of short filaments.
Blends
At this stage, polyester can also be combined with
other fibers to produce a variety of effects.
Polyester and cotton is probably the most famous and popular blend. The
polyester helps the fabric retain its shape and resist stains and
wrinkles. The cotton makes the fabric more absorbent and comfortable.
Polyester is combined with wool to give it
wrinkle-resistance and shape retention in all kinds of weather. Since
polyester is stronger than wool, it increases the durability and life of
the fabric. The wool contributes good draping characteristics and
elasticity.
Polyester and rayon is another popular blend fabric.
Here again the polyester makes the fabric more resilient and durable, and
helps it keep its shape. The rayon adds a different texture, has a good
hand, is good for draping, and is more absorbent.
Polyester and nylon produce a strong fabric because
of nylon's strength and abrasion resistance and polyester's wrinkle-free
properties. This combination produces a yarn that is strong, durable,
stable, easy to launder, and resistant to mildew and insects. Problems
with this blend, however, are that pilling may occur, and it does not have
a very nice hand. Furthermore, since neither nylon nor polyester is very
absorbent, the fabric may feel wet and clammy in warm or humid weather.
Weaving
After the yarns are made, they are shipped out to
textile mills to be woven into fabric. Polyester can be made into both
woven and knitted fabrics (such as the infamous double-knit!)
Finishing Processes
Finally, after the fabric is made, one or more of
the following finishing processes is often used to improve the quality of
the fabric:
- Heat setting--creates a permanent shape
- Singeing--improves the hand, reduces pilling, and
increases smoothness
- Anti-static finish--reduces static electricity
- Water and stain repellency--increases comfort and
makes it easier to clean; also used for rainwear
- Resin finishes--increases ease of care
- Calendaring--increases smoothness and reduces
pilling
- Embossing--creates a design and/or luster
|
|
Background
information
|
Supplier partner
|
|
Be notified of page updates
|
|

wwwswicofilcom2015
Background
Polyester is a synthetic fiber derived from coal, air, water, and petroleum.
Developed in a 20th-century laboratory, polyester fibers are formed from a
chemical reaction between an acid and alcohol. In this reaction, two or more
molecules combine to make a large molecule whose structure repeats throughout
its length. Polyester fibers can form very iong molecules that are very stable
and strong.
Polyester is used in the manufacture of many products, including clothing,
home furnishings, industrial fabrics, computer and recording tapes, and
electrical insulation. Polyester has several advantages over traditional fabrics
such as cotton. It does not absorb moisture, but does absorb oil; this quality
makes polyester the perfect fabric for the application of water-, soil-, and
fire-resistant finishes. Its low absorbency also makes it naturally resistant to
stains. Polyester clothing can be preshrunk in the finishing process, and
thereafter the fabric resists shrinking and will not stretch out of shape. The
fabric is easily dyeable, and not damaged by mildew. Textured polyester fibers
are an effective, nonallergenic insulator, so the material is used for filling
pillows, quilting, outerwear, and sleeping bags.
History
In 1926, United States-based E.I. du Pont de Nemours and Co. began research
into very large molecules and synthetic fibers. This early research, headed by
W.H. Carothers, centered on what became nylon, the first synthetic fiber. Soon
after, in the years 1939-41, British research chemists took interest in the du
Pont studies and conducted their own research in the laboratories of Calico
Printers Association, Ltd. This work resulted in the creation of the polyester
fiber known in England as Terylene.
In 1946, du Pont purchased the right to produce this polyester fiber in the
United States. The company conducted some further developmental work, and in
1951, began to market the fiber under the name Dacron. During the ensuing years,
several companies became interested in polyester fibers and produced their own
versions of the product for different uses. Today, there are two primary types
of polyester, PET (polyethylene terephthalate) and PCDT (poly-1,
4-cyclohexylene-dimethylene terephthalate). PET, the more popular type, is
applicable to a wider variety of uses. It is stronger than PCDT, though PCDT is
more elastic and resilient. PCDT is suited to the heavier consumer uses, such as
draperies and furniture coverings. PET can be used alone or blended with other
fabrics to make clothing that is wrinkle and stain resistant and retains its
shape.
Raw Materials
Polyester is a chemical term which can be broken into poly, meaning
many, and ester, a basic organic chemical compound. The principle
ingredient used in the manufacture of polyester is ethylene, which is derived
from petroleum. In this process, ethylene is the polymer, the chemical building
block of polyester, and the chemical process that produces the finished
polyester is called polymerization.
The Manufacturing
Process
Polyester is manufactured by one of several methods. The one used depends on
the form the finished polyester will take. The four basic forms are filament,
staple, tow, and fiberfill. In the filament form, each individual strand of
polyester fiber is continuous in length, producing smooth-surfaced fabrics. In
staple form, filaments are cut to short, predetermined lengths. In this form
polyester is easier to blend with other fibers. Tow is a form in which
continuous filaments are drawn loosely together. Fiberfill is the voluminous
form used in the manufacture of quilts, pillows, and outerwear. The two forms
used most frequently are filament and staple.
Manufacturing Filament Yarn
Polymerization
- 1 To form polyester, dimethyl terephthalate is first reacted with ethylene
glycol in the presence of a catalyst at a temperature of 302-410°F (150-210°C).
- 2 The resulting chemical, a monomer (single, non-repeating molecule)
alcohol, is combined with terephthalic acid and raised to a temperature of
472°F (280°C). Newly-formed polyester, which is clear and molten, is
extruded through a slot to form long ribbons.
Drying
- 3 After the polyester emerges from polymerization, the long molten ribbons
are allowed to cool until they become brittle. The material is cut into tiny
chips and completely dried to prevent irregularities in consistency.
Melt spinning
- 4 Polymer chips are melted at 500-518°F (260-270°C) to form a syrup-like
solution. The solution is put in a metal container called a spinneret and
forced through its tiny holes, which are usually round, but may be
pentagonal or any other shape to produce special fibers. The number of holes
in the spinneret determines the size of the yarn, as the emerging fibers are
brought together to form a single strand.
- 5 At the spinning stage, other chemicals may be added to the solution to
make the resulting material flame retardant, antistatic, or easier to dye.
Drawing the fiber
- 6 When polyester emerges from the spinneret, it is soft and easily
elongated up to five times its original length. The stretching forces the
random polyester molecules to align in a parallel formation. This increases
the strength, tenacity, and resilience of the fiber. This time, when the
filaments dry, the fibers become solid and strong instead of brittle.
- 7 Drawn fibers may vary greatly in diameter and length, depending on the
characteristics desired of the finished material. Also, as the fibers are
drawn, they may be textured or twisted to create softer or duller fabrics.
Winding
- 8 After the polyester yarn is drawn, it is wound on large bobbins or
flat-wound packages, ready to be woven into material.
Manufacturing Staple Fiber
In making polyester staple fiber, polymerization, drying, and melt spinning
(steps 1-4 above) are much the same as in the manufacture of filament yarn.
However, in the melt spinning process, the spinneret has many more holes when
the product is staple fiber. The rope-like bundles of polyester that emerge are
called tow.
Drawing tow
- 1 Newly-formed tow is quickly cooled in cans that gather the thick fibers.
Several lengths of tow are gathered and then drawn on heated rollers to
three or four times their original length.
Crimping
- 2 Drawn tow is then fed into compression boxes, which force the fibers to
fold like an accordion, at a rate of 9-15 crimps per inch (3-6 per cm). This
process helps the fiber hold together during the later manufacturing stages.
Setting
- 3 After the tow is crimped, it is heated at 212-302°F (100-150°C) to
completely dry the fibers and set the crimp. Some of the crimp will
unavoidably be pulled out of the fibers during the following processes.
Cutting
- 4 Following heat setting, tow is cut into shorter lengths. Polyester that
will be blended with cotton is cut in 1.25-1.50 inch (3.2-3.8 cm) pieces;
for rayon blends, 2 inch (5 cm) lengths are cut. For heavier fabrics, such
as carpet, polyester filaments are cut into 6 inch (15 cm) lengths.
The Future
Following its introduction to the United States in 1951, polyester quickly
became the country's fastest-growing fiber. Easy care of the permanent press
fabric made polyester doubleknits extremely popular in the late 1960s. However,
polyester has suffered an "image problem" since that time, and clothes
made out of polyester were often devalued and even ridiculed. Several new forms
of polyester introduced in the early 1990s may help revitalize the image of
polyester. A new form of polyester fiber, called microfiber, was introduced to
the public in 1991. More luxurious and versatile than traditional polyester,
microfiber fabrics are difficult to tell apart from silk fabrics. Clothing
designers such as Mary McFadden have created a line of clothes using this new
form of polyester. Textile researchers at North Carolina State University are
developing a form of polyester that may be as strong as Kevlar, a superfiber
material used to make bulletproof vests. This type of polyester may eventually
be used as composite materials for cars and airplanes.
Are you looking for a product (yarn or fiber) which is difficult to find such
as PET FDY and DTY 40D/27F (dtex 44 f 27) or some fine high tenacity polyester
multifilament or monofilament yarns please let us know. We love to serve you
well.