|
|
Polyamide Nylon filament yarns and fibers from Swicofil

Polyamide
It is our pronounced
strategy eventually to be able to provide textile companies with all
synthetic yarns and fibers. Since our background however is the field of
nylon and polyester filament yarns please accept that for another
product we may need more time to find a suitable source.
Swicofil is concentrating
on specialities and on providing an excellent and reliable
service - so please do not waste your and other people's time
with mass standard product inquiries with the only goal to get cheapest
quotations. This is not the Swicofil job!
Introduction History:
In September 1931, American chemist Wallace Carothers reported a research carried out in the laboratories of the DuPont Company on “giant” molecules called polymers. He focused his work on a fiber referred to simply as “66,” a number derived from its molecular structure. By 1938, Paul Schlack of the
I.G. Farben Company in Germany, polymerized caprolactam and created a different form of the polymer, identified simply as nylon “6.” DuPont began commercial production of nylon in 1939. The first experimental testing used nylon as sewing thread, in parachute fabric, and in women's hosiery. Nylon stockings were shown in February 1939 at the San Francisco Exposition — and the most exciting fashion innovation of the age was underway. Basic
Information:
Basic Principles of Nylon Fiber Production — The term nylon refers to a family of polymers called linear polyamides. There are two common methods of making nylon for fiber applications. In one approach, molecules with an acid
(COOH) group on each end are reacted with molecules containing amine (NH2) groups on each end. The resulting nylon is named on the basis of the number of carbon atoms separating the two acid groups and the two amines. Thus nylon 6,6 which is widely used for fibers is made from adipic acid and hexamethylene
diamine. The two compounds form a salt, known as nylon salt, an exact 1:1 ratio of acid to base. This salt is then dried and heated under vacuum to eliminate water and form the polymer.
In another approach, a compound containing an amine at one end and an acid at the other is polymerized to form a chain with repeating units of (-NH-[CH2]n-CO-)x. If n=5, the nylon is referred to as nylon 6, another common form of this polymer. The commercial production of nylon 6 begins with caprolactam uses a ring-opening polymerization.
In both cases the polyamide is melt spun and drawn after cooling to give the desired properties for each intended use. Production of nylon industrial and carpet fibers begins with an aqueous solution of monomers and proceeds continuously through polymerization, spinning, drawing, or draw-texturing. |
Properties
Specific weight |
Nylon 6
1.13 - 1.15
Nylon 6.6 1.13 - 1.15
Nylon 6.10 1.09
Nylon 6.12 1.09
Nylon 11 1.04 to 1.05 |
Tenacity |
|
Water absorbtion |
Nylon
6 max. 8,5 - 10 %
Nylon 6.6 max. 8,5 %
Nylon 6.10 max. 3,3 %
Nylon 6.11 max. 2,5 - 3 % |
Moisture regain |
7 % |
Elongation |
50 % |
Melting point |
Nylon
6 210 - 220°C
Nylon 6.6 255-265°C
Nylon 6.10 220°C
Nylon 6.11 195-219°CC |
Flammability UL94 |
3 |
Electrical Resistivity |
5E+13 Ohm-cm |
Solvents |
Phenols and phenol/chlorinated hydrocarbon mixtures. Relatively unaffected
by: hydrocarbons, esthers, ethers, oils, concentrated alkalis |
Decomposed by |
concentrated mineral acids, halogens |
Combustion |
melts, darkens, finally burns with a small flame, easy to extinguish,
giving a white smoke |
Permeability to gases |
O2 ... 0.04
CO2 .. 0.16 to 0.20
N2 ... 0.01 |
Elastic modulus |
Nylon 6 200 to 300
Nylon 6.6 250
Nylon 6.10 400
Nylon 11 500 (daN/mm2) |
|
|
Polyamide Characteristics
- Exceptionally strong
- Elastic
- Abrasion resistant
- Lustrous
- Easy to wash
- Resistant to damage from oil and many chemicals
- Can be pre-colored or dyed in wide range of colors
- Resilient
- Low in moisture absorbency
- Filament yarns provide smooth, soft, long-lasting fabrics
- Spun yarns lend fabrics light weight and warmth
Top of page
|
Applications
- Apparel:
Blouses, dresses, foundation garments, hosiery, lingerie, underwear, raincoats, ski apparel, windbreakers, swimwear, and cycle wear
- Home Furnishings:
Bedspreads, carpets, curtains, upholstery
- Industrial and Other Uses:
Tire cord, hoses, conveyer and seat belts, parachutes, racket strings, ropes and nets, sleeping bags, tarpaulins, tents, thread,
fishing line
General Nylon Fiber Care Tips
Most items made from nylon can be machine washed and tumble dried at low temperatures. Use warm water and add a fabric softener to the final rinse cycle.
Remove articles from dryer as soon as tumbling cycle is completed.
If ironing is required, use warm iron. (For specific care instructions, refer to garment's sewn-in care label.)
Top of page
|
Grades
- flat yarn
- textured yarn
- high tenacity
- monofilament
- staple fibers
- tow
- spun yarns
Top of page
|
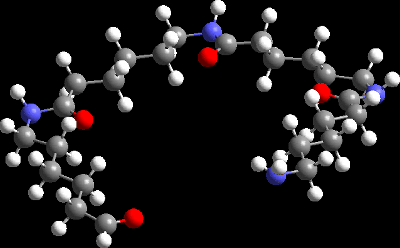 |
Processability Top
of page |
Background
information
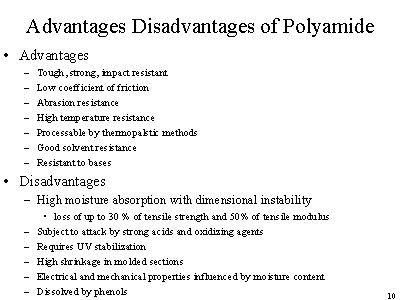
Top of page
|
Specialities
Co-polymer nylon fiber for non-woven
Du Pont has decided to stop the production
of their semidull, heterofil, standard crimp (non-set), ordinary acid
dyeable Nylon 6, 6/6 staple fiber dtex 3.3 / 60 mm cut length type
3100.
We are able to help you with an excellent
alternative of a high quality product in both 3.3 and 6.7 dtex with a cut
length of 51 or 60 mm. For more information please follow
this link
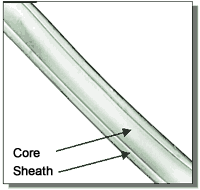
|
|