|
|
Polymethyl methacrylate PMMA

PMMA
Introduction
Polymethyl methacrylate, which is abbreviated as PMMA, is a clear plastic,
used as a shatterproof replacement for glass. On both sides of the Atlantic PMMA
is also marketed as Plexiglas.
PMMA is more than just plastic and paint. Often lubricating oils and
hydraulic fluids tend to get really viscous and even gummy when they get really
cold. This is a real pain when you're trying to operate heavy equipment in
really cold weather. But when a little bit PMMA is dissolved in these oils and
fluids, they don't get viscous in the cold, and machines can be operated down to
-100 oC (-150 oF), that is, presuming the rest of the
machine can take that kind of cold!
PMMA is a vinyl polymer, made by free radical vinyl polymerization from the
monomer methyl methacrylate.
Properties
-
hard
-
rigid
-
transparent (very clear to see through)
-
softening point at 125 deg C
-
tougher than polystyrene but less tough than ABS (acrylobutylstyrene) polymer
-
absorbs very little visible light but there is a 4% reflection at each polymer-air interface for normal incident light.
-
PMMA is a polar material and has a rather high dielectric constant and power factor (what is a power factor??) -
a good electrical insulator at low frequencies but less satisfactory at higher frequencies
-
good water resistance
-
PMMA prepared by free radical polymerization is amorphous and is therefore soluble in solvents with similar solubility parameters such as benzene, toluene, chloroform, methylene chloride, esters, ethyl acetate, and amyl acetate.
-
PMMA has good resistance to alkalis (sodium hydroxide, etc.), aqueous inorganic salts (the Pacific Ocean) and dilute acids.
-
PMMA has a better resistance to hydrolysis than PMA probably by virtue of the shielding of the methyl group.
-
PMMA 's outstanding good outdoor weather resistance is remarkably superior to other thermoplastics.
-
When heated about 200 deg C, decomposition becomes appreciable and at 350- 450 deg C, a nearly quantitative yield of monomer is
readily obtained. Thus, the recovery of monomer from scrap is feasible.
-
Because it's a thermoplastic, it can be molten and molded (at 100 to 150 deg C) into anything we want.
-
Applications
|
Grades
-
flat yarn
-
monofilament
-
fibers
|
|
Processability
-
POF
is strong and very difficult to bend.
There is only a small loss even
when bent to a 25mm radius. Therefore, it can be installed within walls or
other narrow areas. It is also suitable for lighting in tight locations.
-
Installation
work is extremely simple.
There are several methods, but the one
common for transmission is the Hot Plate method. In this method, it takes
advantage of the fact that the material used is plastic, so that fiber
ends are heated and softened, then pushed against a mirrored surface. The
process is quick and can be repeated with very little deviation.
Therefore, installation is simple even for those who have never handled
optical fiber.
-
Normally,
a 650nm (red) LED is used as the light source for POF optical transceiver
modules.
Since
this is within the visible light spectrum, it acts as an eye safety
feature because the user can easily tell when he/she is in danger of
directly viewing the light beam. Also, since 650nm will be the wavelength
used for a large number of DVD light sources, we can expect the cost to
drop even further.
-
POF
is not suitable for long-distance transmission.
compared
with quartz fiber, there is a large transmission loss. However home and
office applications do not require transmission over great distances,
having a need for ease-of-use, low cost, and stability instead. POF is
best suited for use in these environments.
-
Since
POF is strong against vibration and bending, in addition to its
conventional uses in high-speed trains and automobiles it has also
recently been applied to car networks inside the vehicle due to an
increasing multimedia demand from drivers.
- Since
POF transmits very little infrared light, it can be used for cold
lighting (lighting that do not produce heat), for semiconductor
manufacturing equipment and the lighting displays of artwork.
-
|
Background
information
Principles
of Optical Fiber
Optical fiber
transmits light. But, what prevents the light from escaping from the fiber?
The
answer is based on a principle that we experience every day.
While
swimming at the beach as a child, have you ever thought that you were safely in
shallow water only to be surprised to find that it was too deep to touch the
bottom? When you look straight down into a clear lake or puddle, you can see its
bottom. However, when you view it at an angle and look off into the distance,
the distant scenery is reflected upside down. This is caused by the difference
in the index of refraction between the water and air, which you probably learned
about in grade school.
Although
optical fiber appears to be only a simple thread, it is actually composed 2
structures similar to water and air. The area where light is transmitted is
called the core, and the external area is called the clad.
When
light enters the area between 2 materials with different indexes of refraction
(boundary face), the light will be either entirely reflected or a portion of it
will be refracted, depending on the angle.
If
the light can be kept at an angle where it is entirely reflected, it will
become trapped inside and transmitted along the fiber.
|
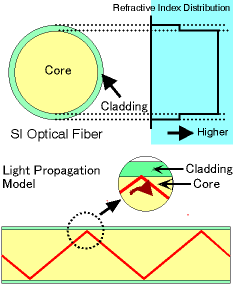 |
|
Our
supplier partner
|
|