|
|
Milk fiber

Milk Fiber
Introduction
Foreword
All through the years, experts have been devoted to the
researches on improved fibers and at present they have succeeded in the
development of the globally advanced milk protein fiber,
a milestone in the international textile industry. Up to now, this kind of
fiber was only produced in Japan.
The emergence of milk protein fiber updates the
traditional definition of animal protein fiber. Being the optimal
combination of nature and hi-tech, it is more accommodated to the needs of
people’s modern lifestyle.
Milk protein fiber is dewatered and skimmed milk which is manufactured into the
protein spinning fluid suitable for wet spinning process by means of new
bio-engineering technique. Milk protein fiber has passed Oeko-Tex Standard 100
green certification for the international ecological textiles.
Milk protein fiber is healthy for skin, comfortable, with bright colors due to
good dye ability, etc. The milk protein fiber can be spun purely or spun with
cashmere, silk, spun silk, cotton, wool, ramie and other fibers to weave fabrics
with the features of milk protein fiber. It can also be used to create top-grade
underwear, shirts, T shirts, loungewear, etc. to satisfy people’s pursuit of
comfortable, healthy, superior and fashionable garments.
The milk protein fiber is a fresh product as a superior green, healthy and
comfortable fiber, which will certainly become popular goods in the market as
new favorite of the textile trade.
Properties
Good moisture, absorption and conduction:
The fiber base body
does not have regular channels, which makes the milk fiber have as
fine moisture absorption as natural fiber and better moisture
conduction than synthetic fibers - milk fiber is both comfortable and
permeable.
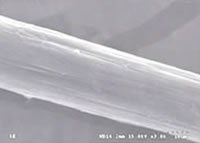
Vertical picture of fiber
Horizontal picture of fiber
Main technical indexes of milk protein fiber
No
|
Item name
|
Index
|
1
|
Fiber tenacity
(dtex)
|
0.8-3
|
2
|
Breaking
tenacity (cN/dtex)
|
2.5-3.5
|
3
|
Breaking
elongation rate (%)
|
25-35
|
4
|
Modulus
(cN/dtex)
|
60-80
|
5
|
Standard
moisture regain(%)
|
5.5
|
6
|
Specific
resistance
|
1.5×104
|
7
|
Static friction
coefficient
|
0.187
|
|
Dynamic
friction coefficient |
0.214 |
8
|
Color fastness
to washing
|
4-5 grade
|
|
Fastness to crocking
|
4-5 grade
|
|
Fastness to perspiration
|
4-5 grade
|
|
Color
fastness to light |
4 grade |
9
|
Pilling
resistance
|
3 grade
|
10
|
Content of formal
dehyde
|
0
|
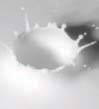
Functional comparison of milk protein fiber fabrics
1). Permeability
Knit fabric
|
Milk protein fiber
|
Polypropylene fiber
|
Polyester
|
Polyamide
|
Acrylic
|
Silk
|
Permeability
|
1.78
|
0.64
|
0.775
|
0.645
|
0.98
|
1.215
|
2). Wet conduction
Knit fabric
|
Milk protein fiber
|
Polypropylene fiber
|
Polyester
|
Polyamide
|
Acrylic
|
Silk
|
10minutes wicking rate
|
3.78
|
3.10
|
4.11
|
0
|
2.06
|
0.85
|
Wetting area (cm2)
|
8.170
|
15.54
|
13.9
|
0
|
4.6
|
1.04
|
Wetting volume (cm3)
|
0.430
|
0.653
|
0.695
|
0
|
0.298
|
0.058
|
3). Heat retention
Fabric
|
Thermal resistance (clo)
|
Heat transfer coefficient (kal/m.h.)
|
Heat retention rate(%)
|
Milk protein fiber knit fabric
|
0.2491
|
26.08
|
28.5
|
Acrylic knit fabric
|
0.1985
|
33.33
|
24.02
|
Cotton knit fabric
|
0.2639
|
25.98
|
29.71
|
Wool knit fabric
|
0.3341
|
19.3
|
36.26
|
4). Antistatic property
Fiber
|
Milk protein fiber
|
Polyester (deoiled)
|
Polyamide (deoiled)
|
Acrylic
|
Silk
|
Mass specific resistance (lg pm) (Relative humidity is 65%)
|
9.1
|
14
|
14
|
9.12
|
9.8
|
5). Friction coefficient
Knit fabric
|
Milk protein fiber
|
Cotton
|
Silk
|
Friction coefficient
|
0.214
|
0.298
|
0.332
|
6). Bending elastic modulus
Knit fabric
|
Milk protein fiber
|
Cotton
|
Silk
|
Bending elastic modulus
|
0.33
|
3.65
|
1.47
|
7). Drapability
Knit fabric
|
Milk protein fiber
|
Cotton
|
Silk
|
Drape coefficient (%)
|
8
|
16
|
10
|
Milk protein fiber can be dyed under the normal temperature, and other
characteristics are good.
Sample Name:
|
Milk fabric
|
Sample Quantity:
|
30*30cm
|
Sample description
|
red
|
Environmental condition:
|
Temperature:20 ± 2 degr C
Humidity :65 ± 3% RH
|
Ref. Documents For the test
|
GB/T 8427-1998 GB/T 4802.3-1997 GB/T 3920-1997
GB/T 3921-1997 GB/T 3922-1995FZ/T 01057-1999
|
Test conclusion
|
Fiber content
|
Milk60%/wool40%
|
Anti-light color fastness
|
+4
|
Anti-friction
|
3
|
3
|
Anti-washing
|
4-5
|
Anti-sweat (alkali)
|
4-5
|
Anti-sweat (acid)
|
4-5
|
Tested by National Inspection and Testing Center for Fiber Products
Quality, the shell fabric is washing and perspiration resistant, the
color fastness to light reaches grade 4-5 and the pilling resistance
goes up to third grade.
Applications
The milk protein fiber moistens skin and it is healthy and
bacteriostatic - it is the perfect material to produce
underwear. The important ingredients of milk protein fiber are
milk casein proteins, which can nourish and lubricate the
skin. The milk protein contains the natural humectant factor,
which can capture moisture and this will maintain the skin’s
moisture - it makes the skin tender and smooth and reduce
wrinkles – peoples’ dream of taking milk baths can be
realized.
- T-Shirts
- Underwear
- Ladies outerwear
- Sportswear
- Sweaters
Milk protein fiber reduced the
cost of cashmere products. At present, the whole industrial
process from fiber spinning, weaving, printing and dyeing to
ready-made garments has been combined, milk yarn with
different specifications has been developed, and milk
underwear, milk cashmere sweaters, T-shirts and so on have
already appeared on the market...
|
Grades
- fibers
- tow/tops
- spun yarns
|
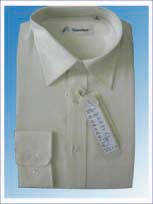 |
Processability
Main
process of milk protein fiber
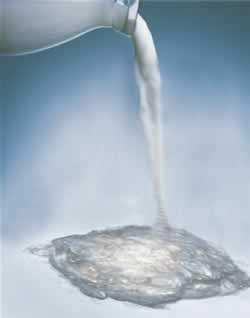
To make milk protein
fiber, milk is first dewatered and skimmed, then by means of
new bio-engineering technique, the protein spinning fluid
suitable for a wet spinning process is manufactured, then
finally the new high-grade textile fiber is made. It
combines the advantages of natural fiber and synthetic fiber
- the protein fiber is a kind of fresh fiber with healthy
function.
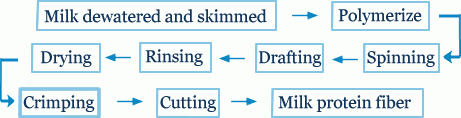
The milk protein fiber contains
eighteen amino-acids, which is beneficial to human’s
health and has the functions of nourishing and taking care
of skin.
Kinds
and content of amino-acid in milk protein
fiber
Kinds of
amino-acid
|
Actual data
|
Kinds of
amino-acid
|
Actual data
|
Aspartic acid
|
2.039
|
Methionine
|
0.7587
|
Threonine
|
0.9918
|
Isoleucine
|
1.101
|
Serine
|
1.429
|
Leucine
|
2.493
|
Glutamic acid
|
5.549
|
Tyrosine
|
1.572
|
Pro.
|
2.529
|
Phe.
|
1.331
|
Glycocoll
|
0.5259
|
Lysine
|
2.289
|
Alanine
|
0.9037
|
Histidine
|
0.8602
|
Cystine
|
0.0815
|
Arginine
|
0.9246
|
Val.
|
1.71
|
Tryptophan
|
0.1831
|
Tested by SGS-CSTC Standards
Technical Services Co. Ltd Shanghai Branch , the content of
amino acid is 30.34%.
Technical infos on how to
work milk fibers can be obtained from us.
|
Background
information
The wet spinning
technology, a unique spinning solvent is used, micro-
zinc ions are is embedded in the fiber, after drying
and after treatment, zinc oxide is produced, therefore it is
bacteriostatic and durable.
Item
|
Test result
|
Golden yellow
staphylococcus
(ATCC NO.6538) |
Restrain
>3.86(99.9986)
Sterilization
> 1.96(98.9011) |
colon bacillus
(ATCC NO.8099) |
Restrain
>5.17(99.9993)
Sterilization
> 2.03(99.0741) |
white Beads
germ
(ATCC NO.8099)
|
Restrain
>3.84(99.9855)
Sterilization
>1.88(98.6667) |
Tested by China National Textiles
Quality Supervision Testing Center, the
bacterial value of golden yellow staphylococcus is greater
than 99.9986, the bacterial value of colon bacillus is
greater than 99.9993 and the bacterial value of white Beads
germ is greater than 99.9855.
Property
comparison between milk protein fiber and other
textile fiber
Property
|
Milk
protein fiber
|
Cotton
|
Silk
|
Wool
|
Length
(mm)
|
38
|
25-39
|
-----
|
58-100
|
Fineness
(dtex)
|
1.52
|
1.2-2.0
|
1.0-2.8
|
6-9
|
*Dry
tensile strength (CN/dtex)
|
2.8
|
1.9-3.1
|
3.8-4.0
|
2.6-3.5
|
*Dry
breaking elongation rate (%)
|
25-35
|
7-10
|
11-16
|
14-25
|
Wet
tensile strength (CN/dtex)
|
2.4
|
3.2
|
2.1-2.8
|
0.8
|
Wet
breaking elongation rate (%)
|
28.8
|
13
|
27-33
|
50
|
Friction
coefficient (static)
|
0.187
|
|
0.52
|
0.24
|
Friction
coefficient (dynamic)
|
0.214
|
|
0.26
|
0.384
|
Logarithm
of mass specific resistance (Wg/ cm2)
|
9.1
|
6.8
|
9.8
|
8.4
|
*Initial
modulus (CN/dtex)
|
60-80
|
60-82
|
60-80
|
44-88
|
Moisture
regain (%)
|
5-8
|
7-8
|
8-9
|
15-17
|
Specific
weight (g/cm3)
|
1.22
|
1.50-1.54
|
1.46-1.52
|
1.34-1.38
|
* The intensity of fiber
breakage and mould are moderate, it is great to
extend, the spinning and weaving performance is good.
Some historic background information
Casein [milk] protein
Casein dates back many centuries when it was used as a binder for
paints -- paint with casein applied to 14th and 15th century churches
still appears bright and unfaded.
Proteins are obtained from skim milk, evaporated milk and condensed
milk. There are about three pounds of casein in every 100 pounds of
milk.
When cut to staple-length fiber casein has many properties of wool. Fibers
are white, fluffy, springy and have a pleasant odor. When blended with
other fibers casein added a soft draping quality and resiliency to
fabrics. Fiber was blended with wool for creating felt and with spun
rayon, wool, mohair and cotton for attractive woven and knitted
fabrics in a variety of weaves, textures and prints.
Even though casein fiber lacks certain desirable qualities of wool it
was a way to replace wool at a lower cost. When mixed with rayon and
wool, casein helped in the conservation effort during WWII as a wool
substitute.
Casein fibers cannot be distinguished from wool fibers by chemical or
burning tests, only by microscope. Because chemical composition is so
similar, casein burns like wool with odor of burning hair, has no
surface scales like wool but is smooth and round when viewed under a
microscope, is damaged readily by alkalis and mildews easily.
Though caseins can be laundered with care the same as wool, they loose
strength when wet and must be handled gently. They cannot be kept damp
for any length of time due to quick mildewing. Three successful brand names
were Aralac in America and Lanital and Merinova in Italy.
|
Ground casein is
poured into trap door, treated with chemicals and heated in huge vats
to form a solution which is forced through spinnerets; washed, dried,
cut into staples and baled to yarn-making plants for spinning and
blending. - America's Fabrics
Textured drapery
made from soft casein yarns combined with other fibers. - America's
Fabrics
Montgomery Ward's
S/S 1942 catalog featured classic felt styles of 94% new wool and 6%
casein fiber. Colors choices were black, flag red, navy, dusty rose,
dusty blue and beige. $2.48 and $3.98 respectively.
|
Lanital
was the first successful protein fiber from milk casein. Antonio
Feretti was granted a patent for this fiber from the Italian
government in 1935. It was named Lanital [lana = wool +ital = Italy],
and manufactured by Snia Viscosa which called the fabric a fancy
rayon. It lasted into the early 40s and superceded by Merinova which was used to blend with rabbit hair in the production of felts.
Merinova was discontinued in the late 1960s.
Fibers of both fabrics were very similar to wool and could be dyed by
the same processes, and like wool they were easily damaged by alkalis.
Both had a resilient wooly feel but were not as strong and firm nor as
elastic as wool. Moths would not attack and shrinkage was not as much
as wool but fibers mildewed easily when damp, an inherent
characteristic of protein fibers as noted earlier.
|
Cross sectional
view of Lanital under a microscope. - Kansas State Ag Bulletin 300
|
Aralac
A patent was granted in 1937 to the United States Department of
Agriculture for making a casein fiber by a somewhat different method
than Lanital. Aralac was developed by the American Research
Associates, a scientific research division of the National Dairy
Products Corp.
A useable fiber was developed and ready for the market in 1940, just
in time to serve as a wool substitute during WWII. Its name was
derived from ARA = American Research Associates + lac = Latin for
milk.
Aralac was blended with rabbit fur in making felt hats and with wool,
mohair, rayon and cotton in varying proportions for fabrics and
garments. Although clothing in this fiber was available as late as
1947, the impact of man-made fibers following the war caused the
demise of this fiber in 1948 as it could not compete with the low
price of new synthetics. Plus when damp, this fabric smelled like sour
milk, causing many consumer complaints, a quite common, familiar
ailment within the casein family.
|
R-53
appeared around
1941; R for research and 53 indicating it was the 53rd fiber tested in a
search for a fiber which was suitable to manufacture felt hats. This fiber was
finer than Aralac and was used to blend with rabbit fur in making felt for
hats. Little information is available. It was listed by this name as late as
1953 but seems to have disappeared. Possibly the fiber might have been renamed
or absorbed by Merinova or failed to survive as a competitor.
|
Caslen
was a trademark of Plastic Products, a division of Rubberset. It
was developed as a curled and resilient replacement for horsehair in
upholstery. It appeared on the market in the late 1940s and according to
glossary listings, was off market by the early 60s. Another brand from Great
Britain was Fibrolane, discontinued in 1965.
|
|
Our
supplier partner
Harvest |
|
|