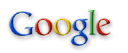
Search Swicofil Site with Google Search
(please click on Logo above)
|
|
Polyimide

Polyimide
Introduction
Polyimide (abbreviated PI)
is polymer of imide monomers. Polyimides have been in mass production since
1955. With their high heat-resistance, polyimides enjoy diverse applications in
end uses demanding rugged organic materials, e.g. high temperature fuel cells,
displays, and various military roles.
Properties
Thermosetting polyimides are known for thermal stability, good
chemical resistance, excellent mechanical properties, and characteristic
orange/yellow color. Thermoset polyimides exhibit very low creep and
high tensile strength. These properties are maintained during continuous
use to temperatures of up to 452 °C and for short excursions, as high as
704 °C. Polyimides are inherently resistant to flame combustion and do
not usually need to be mixed with flame retardants. Typical
polyimide parts are not affected by commonly used solvents and oils —
including hydrocarbons, esters, ethers, alcohols and freons. They also
resist weak acids but are not recommended for use in environments that
contain alkalis or inorganic acids.
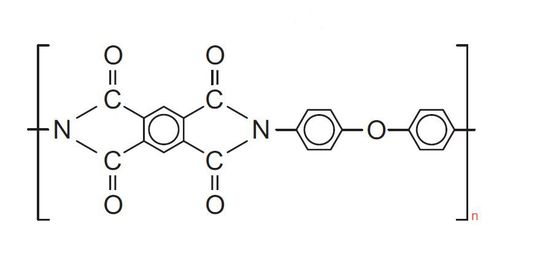
The general index of
oru ASPIŽ polyimide
fiber is as follows,
Fineness 1.5~6 dtex,
Density 1.41 g/cm3 ;
Breaking strength >4.0 cN/dtex;
Elongation at break 10~30%;
Continuous use temperature 260℃;
Decomposition temperature 560℃;
Limiting oxygen index (LOI) 38%;
Applications
Polyimide materials are
lightweight, flexible, resistant to heat and chemicals.
Therefore, they are used in the electronics industry for
flexible cables, as an insulating film on magnet wire and for
medical tubing.
In coal-fired power
plants, waste incinerators or cement plants, polyimide fibres
are used to filter hot gases. In this application, a polyimide
needle felt separates dust and particulate matter from the
exhaust gas.
Polyimide is also the
most common material used for the reverse osmotic film in
purification of water, or the concentration of dilute materials
from water, such as maple syrup production.
Multi-layer insulation
used on spacecraft is usually made of polyimide coated with thin
layers of aluminum. The gold-like material often seen on the
outside of spacecraft is actually single aluminized polyimide,
with the single layer of aluminum facing in. The yellowish-brown
polyimide gives the surface its gold-like color.
End uses Aerospace: Jet
engines and compressor parts, seals, impellers for aircraft,
aircraft engines (sandwich constructions with titanium alloys),
insulation of the spacecraft and the astronauts space suits
against radiation, heat or cold exposure, radomes.
Electrical and
electronics industry: insulating, electronic connectors,
bobbins, wire and cable jacketing, the base material for printed
circuit boards.
Automotive and machinery
industry: piston rings, valve seats, wheels, bearings, sliding
and guiding elements, pads, carburetor body.
Other: Fibers for
refractory protective suits.
|
Grades
- flat yarn
- fibers
- tow/tops
- spun yarns
|
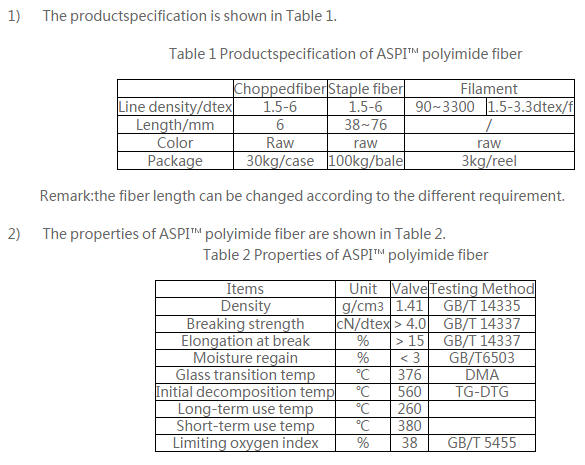 |
Processability
|
Background
information
|
Our
supplier partner
|
|
|